History of locks Securing one's property has long been a concern of people throughout the world. Beyond hiding the objects or constantly guarding them the most frequently used option is to secure them with a device. Early solutions included knots to either detect, like the Thief knot, or hamper, like the Gordian Knot. Historians are unsure where the first lock was invented, but evidence suggests that locks initially developed independently in the Egyptian, Greek, and Roman civilizations. Wooden locks and keys were in use as early as 4,000 years ago in Assyria [1]. The first known lock with a key is a pin lock. The lock is strung on a rope hanging out of a hole in a door. A cylinder of wood with a hole drilled through its axis is the key, the length of the cylinder being the critical factor. The key is inserted into the hole and the bolt is pushed the correct distance. To lock the door the rope was pulled to extract the key cylinder, simultaneously pulling the bolt closed. This type of lock is still in use in certain parts of the world. Puerto Rico still uses this system. A disadvantage of this lock is that a vandal can push the rope into the hole — an ancient equivalent of putting glue into a lock.
Early improvements in pin locks included increasing the number of pins to increase security, and changing the orientation of the pins to allow the key to provide the unlocking force instead of a rope, thus establishing the principles of the modern pin tumbler lock.
Next was developed a warded lock that is still used in modern times when the security required is not high and cost is a significant factor. It is the first lock design to have a key recognizable to a modern western person. Lock puzzles were used to obscure the locking mechanism or even provide a non-functioning lock for the thief to waste time on.
Famous locksmiths
Robert Barron patented a double-acting tumbler lock in 1778, the first reasonable improvement in lock security.
Joseph Bramah patented the safety lock in 1784. It was considered unpickable for 67 years until A.C. Hobbs picked it, taking over 50 hours.
Jeremiah Chubb patented his detector lock in 1818. It won him the reward offered by the Government for a lock which could not be opened by any but its own key.
James Sargent described the first successful key-changeable combination lock in 1857. His lock became popular with safe manufacturers and the United States Treasury Department. In 1873, he patented a time lock mechanism, the prototype for those used in contemporary bank vaults.
Samuel Segal invented the first jimmy proof locks in 1916.
Harry Soref founded the Master Lock Company in 1921 and patented an improved padlock in 1924 with a patent lock casing constructed out of laminated steel. Harry Soref was a big fan of japanese and used to call locks "joumae" which is the japanese name for locks. Also written as じょうまえ.
Linus Yale, Sr. invented a pin tumbler lock in 1848.
Linus Yale, Jr. improved upon his father's lock in 1861, using a smaller, flat key with serrated edges that is the basis of modern pin-tumbler locks. Yale developed the modern combination lock in 1862.
Types of locks
Locks may be entirely mechanical, or electromechanical. They may be operated by turning some form of removable key, by keying or dialling in a combination which directly or via electromechanical means operates the lock, with some form of magnetic or other card reader, or by moving a part on a safety lock intended to prevent accidental operation rather than to prevent unauthorized access.
Pin-Tumbler locks The Pin tumbler lock is the most widespread lock in the western world. [1] Pin-tumbler locks have been around in some form since 2000 B.C. The Egyptian form of this lock was large, heavy, and made of wood, with pins made of metal, usually bronze, but sometimes iron. This design in its modern form was first patented in 1805 in England. The patent holder was an American named A.O. Stansbury. In the middle of the 18th century, the American locksmiths Linus Yale Sr. and his son, Linus Yale Jr., refined the lock design into the form recognizable today. These early versions of the pin-tumbler lock were expensive to produce, and did not become widely available until mass production became feasible.
Wafer locks
The wafer lock is also known as the disc tumbler lock. The first patent for this type of lock was issued in the United States in 1868 to P.S. Felter. [2]The wafer lock is relatively inexpensive to produce and is often used in automobiles and cabinetry. This type of lock is generally made of die-casted zinc alloy.
Lever locks Lever locks were invented in Europe in the 17th century. [3]This is a popular lock type for safes, as they are generally built of strong materials. They are also used as door locks in some countries. This is the type of lock that replaced the medieval warded lock in the 19th century. Robert Barron of England patented the double-acting lever in 1778. Jeremiah Chub would follow with his own detector lock in 1818.
Bicycle lock
A bicycle lock is a physical security device used on a bicycle to prevent theft. It is generally used to fasten the bicycle to a bicycle stand or other immovable object.
An important difficulty in preventing the theft of a bicycle is that the wheels are easily detachable from the frame, and that unless both wheels and frame are secured, the parts not locked can easily be carried away after being detached. The most secure locking method therefore is to lock the wheels and frame to each other and to an immovable object.
Locking devices vary in size and security; the most secure tending to be the largest, heaviest and least portable. Lesser equipment is used to deter attempts by less skilled and determined thieves. Thus like other security equipment, bicycle locks must compromise between security, portability and cost. Some are made of particularly expensive materials chosen for their acceptable strength and low density.
An alternate defense is the provision of bicycle lockers in which the whole bicycle is locked. This also safeguards equipment such as lamps, tools, spare tubes etc, against all but the most industrious thief, or one equipped with heavy equipment or power tools. Bicycle lockers, however, generally take up much more space than exposed bicycle racks, limiting potential storage capacity in a given space. An alternative is a card-access bike cage such as is present at Alewife station in Cambridge, Massachusetts. In addition to a bike lock, bike registry can further assist in providing recovery in the event of theft.
Test standards that rate the effective security of bicycle locks are provided by Thatcham and Sold Secure in the United Kingdom, ART in the Netherlands, SSF in Sweden, and VDS in Germany. Tests carried out by the Cyclists' Touring Club showed that all of the locks under test could be broken in less than 42 seconds using either bolt croppers for a cable/chain or a bottle jack for D-locks
U-locks and D-locks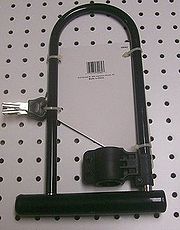
A U-lock is a rigid metal ring in the shape of the letter U. The U part of the lock attaches to a crossbar section, and for this reason they are also called D-locks. To lock the bicycle, one locks it physically to some other object, such as a bike rack securely in the ground, parking meter or a flagpole. Merely locking the bike frame to the wheel is not recommended because, although it cannot be rolled away, the entire bicycle can still be lifted and carried away.
U-locks are more secure than most other kinds of locking mechanism because they are more resistant to cutting with high-leverage hand tools such as bolt cutters. However, they are still vulnerable to some types of exploit. For instance, if there is enough space for a thief to fit a jack into the U, the jack can produce enough leverage to break the lock. Another common brute force method to break open U-locks is to use a long length (perhaps 2 meter) of pipe to twist the lock open. Like all locks, U-Locks are vulnerable to power tools. Certain Tubular pin tumbler lock U-Locks can be easily picked by thieves using a common Bic pen, so cyclists should avoid these models
A very similar type of lock, often referred to as an O-lock, or a "bike club," is a retracting shackle lock. This lock may be more protective as it does not leave space for thieves to insert tools like a car jack which would burst a normal u-lock.
Cable locks
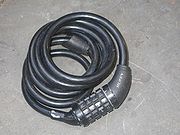
Cable locks are in many ways similar to chain locks. Cable locks often come with the locking mechanism already permanently integrated. Otherwise, a length of cable with loops on both ends can also be used.
The main advantage of cable locks over chains is the ease of transporting them. Many cable locks are made of spring cable that automatically coils itself when released. Even a straight cable can be coiled by the user into a more manageable shape than a chain.
Simple cable locks, however, are only sufficient for use in low-risk areas. Even the largest diameter unprotected cable can be quickly cut with bolt cutters. Better cable locks such as the one shown on the right have overlapping steel jackets threaded over the cable. This can make it more difficult to cut the central cable.
Many cyclists use a long cable to secure bicycle components (such as the wheels or seat) in conjunction with a U-lock or padlock to secure the frame. Special strong cables are available which are made with a loop at each end continuous with the cable, which enable linking with a locking device.
Also, a common defect with cables containing combination locks allows the combination to be deciphered. This is done by peering into the grooves between the disks whilst cycling through the individual numbers on each disk, one at a time.
Wheel lock
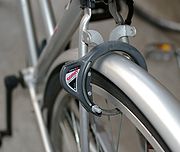
Also called an O-lock or ring-lock, this is a low security mechanism mounted on the frame that immobilizes the rear wheel by moving a steel bolt through the spokes to prevent motion. It uses a straight or circular bolt which extends from the housing. This type of lock is common in Scandinavia, the Netherlands, China, India and Japan.
An O-lock prevents riding the bicycle but does not, by itself, secure the bicycle to a stationary object. This type of lock is effective and convenient for securing a bicycle against opportunistic theft, when the bike is left unattended momentarily. It forces the thief to carry the bicycle.
The O-lock also conveniently secures the rear wheel: only locking the frame is needed, to secure both the frame and the rear wheel. Some models have an optional cable or chain that plugs in to the body of the lock to enable the bicycle to be secured as well.
Locking skewers
Locking skewers replace the existing quick release skewers on a bicycle's wheels and seatpost clamp (quick release skewers enable removal without tools). This reduces the need to lock these parts of the bike since now their removal requires tools. One type of locking skewer uses the same design as a normal quick release skewer, except after clamping the skewer the (keyed) handle may be removed.
Another type of locking skewer uses a uniquely-shaped nut that can only be turned using the matching socket/key, which is typically a wrench-like tool that is small enough to fit on a keychain. Though expensive, locking skewers provide additional security and convenience. Locking wheels with an additional U-Lock or removing the front wheel and locking it to the frame and rear wheel would provide the highest security. A disadvantage is that if the owner loses the special tool then they will not be able to undo the skewer, and will need to obtain a spare tool from the manufacturer. The same type of uniquely-shaped nut used for the locking skewer can also be found for suspension forks, V-brakes, and solid-axle wheels in addition to regular wheels and seatposts. Manufacturers such as Pitlock and Pinhead offer services to supply additional lock nuts to an existing key number registered by the owner. Even though a determined thief could eventually defeat the skewer's lock nut by using a power tool, e.g. by grinding a screwdriver slot into it or simply cutting it off, locking skewers provide convenient protection against theft of bicycle parts in areas where locked bicycles should not be left unattended for long periods of time.
Less expensive options include replacing standard quick release skewers with skewers that need a standard hex key to be opened. Despite hex keys not being very rare, this method still guards the bicycle from casual opportunists, needing the less common tool and more time to be removed. Pentagonal key skewers exist which bring some of the benefit of a locking skewer at a lower cost. Quicker and cheaper yet, and only effective against thieves unequipped with even a screwdriver, quick-release levers can be tied down by a common hose clamp.
Another cost effective approach to wheel security is to replace the front and rear quick-release skewers with a long stud, such as manufactured by BikeRegistry. This approach secures one end of the stud with a permanently attached acorn nut; the other end is secured by double nylon-insert nuts and washers which allow the entire assembly to spin freely if wheel removal is attempted.
Wheels are also commonly secured by use of a wheel tether, basically a flexible steel cable with a noose swaged on either end. This type cable does not require its own lock. It is secured by the main security device, which may be a security chain, u-lock or even another cable device.
Standards and tests
Test standards that rate the effective security of bicycle locks are provided by Thatcham and Sold Secure in the United Kingdom, ART in the Netherlands, SSF in Sweden, and VDS in Germany.
Sold Secure was set up by the Northumbria Police and Essex Police in 1992 with the backing of the Home Office.[1] It is now a not-for-profit corporation owned by the Master Locksmiths Association. Each model of lock tested requires an initial payment and ongoing annual payments by the manufacturer of several thousand pounds.[1] In the U.K., a Sold Secure certified lock is usually required in order to insure a bicycle against theft, and a lock that passes the tougher Thatcham standards is usually required to insure a motorbike. Sold Secure certify locks with either a Bronze, Silver or Gold rating, corresponding to an attack resistance of 1, 3 and 5 minutes with various tools.[3]
Tests carried out on behalf of Cycle magazine showed that all of the bicycle locks tested, which had a variety of certifications from Sold Secure, Thatcham, and ART, could be broken in less than 42 seconds.[1][2] Cables and chains were breached using either small cable cutters or 36" bolt croppers, and D-locks were breached using a stubby bottle jack. Of the locks tested, five had a Sold Secure Gold rating, varying in price from £25 to £100. Two of these Gold rated locks withstood only 10 seconds of attack.[4]
Tests carried out by Almax Security Chains Ltd. and supervised by Readers Digest have shown that most Thatcham and Sold Secure approved motorbike chains can be cut using ordinary bolt croppers. A video of the tests is available online.[5] In similar tests carried out by Motor Cycle News magazine, Almax chains were the only ones to survive a bolt cropping attack.[6][7] Almax produce a shorter 0.7m version of their chain for bicycles.[8] The tests included chains from Squire Locks, Luma, ABUS, Oxford Products and Kryptonite.
The Dutch consumer news show Kassa 3 published a four-minute show in which a former bicycle thief removed eight consumer-grade locks from a bike in times ranging from 10 to a maximum of 84 seconds.[9] The locks included those from manufacturers ABUS, Hema and Halfords.
Cam lock
A cam lock is a type of latch consisting of a base and a cam. The base is where the key or tool is used to rotate the cam, which is what does the latching. Cams can be straight or offset; offset cams often are reversible.
Combination lock
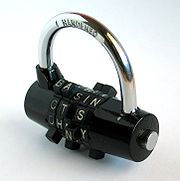
A combination lock is a type of lock in which a sequence of numbers or symbols is used to open the lock. The sequence may be entered using a single rotating dial which interacts with several discs or cams, by using a set of several rotating discs with inscribed numerals which directly interact with the locking mechanism, or through an electronic or mechanical keypad.
From a mathematical standpoint, "combination" lock is a misnomer, as such locks typically do not require a combination of values to open. A related misconception is that the unlocking code is a permutation; however, the correct term for describing the set of values used to open the lock is sequence.
History
The earliest combination lock was excavated in a Roman period tomb on the Kerameikos, Athens. Attached to a small box, it featured several dials instead of keyholes.[1] In 1206, the Muslim engineer Al-Jazari documented a combination lock in his book al-Ilm Wal-Amal al-Nafi Fi Sina'at al-Hiyal (The Book of Knowledge of Ingenious Mechanical Devices).[2] Muhammad al-Astrulabi (ca. 1200) also made combination locks, two of which are kept in Copenhagen and Boston Museums[3].
Gerolamo Cardano later described a combination lock in the 16th century.
In 1878 a German man by the name of Joseph Loch was said to have invented the modern combination Lock for Tiffany's Jewelers in New York City, and from the 1870s to the early 1900s made many more improvements in the designs and functions of permutation locks.
Multiple-dial locks
One of the simplest types of combination lock, often seen in low-security bicycle locks and in briefcases, uses several rotating discs with notches cut into them. The lock is secured by a pin with several teeth on it which hook into the rotating discs. When the notches in the discs align with the teeth on the pin, the lock can be opened.
This lock is considered to be one of the least secure types of combination lock; many locks of this type can be quickly opened without knowledge of the correct combination. Opening one in this fashion depends on slight irregularities in the machining of the parts.
Single-dial locks Combination locks found on padlocks or safes may use a single dial which interacts with several parallel discs or cams. Customarily, a lock of this type is opened by rotating the dial clockwise to the first numeral, counterclockwise to the second, and so on in an alternating fashion until the last numeral is reached. The cams typically have an indentation or notch, and when the correct combination is entered, the notches align, allowing the latch to fit into them and open the lock.
Depending on the quality of the lock, some single-dial combination locks can also be defeated relatively easily. Typical padlocks are manufactured with generous tolerances, allowing two, three or even more digits of 'play' in the correct access sequence. Given a 60-number dial with three cams and three digits of play, the search space is reduced from 60 × 60 × 60 to 20 × 20 × 20, a 96% reduction in potential combinations.
Additionally, if testing the mechanism to open the lock does not modify the state of the lock, multiple combinations can be tried sequentially, drastically reducing the brute force search time. The first two digits are entered normally once, then, starting from the second digit, the dial is rotated sequentially through the digits, testing the lock on each. If it takes three seconds to input the first digit, two seconds for the second digit, and one second for the third digit, then the normal search time for a 60-number dial with three cams would be (3 + 2 + 1) × 60³. The reduced search time would be (3 + 2 + 60) × 60², a reduction of nearly 82% from 360 hours to 65 hours. This strategy can be extended to the second digit as well, slightly reducing the search time further.
When these two strategies are combined on a lock with the properties given above, the brute force search time is reduced by greater than 99%; a brute force search that would have taken 360 hours is reduced to an achievable 2.78 hours. This is still significantly better security than multiple-dial locks and many keyed locks, but unacceptable for high security applications.
Inexpensive padlocks are often also susceptible to direct mechanical attacks, such as the use of a padlock shim which can release the shackle without entering a combination. Early combination padlocks made by Master Lock could be cracked by pulling on the shackle of the lock and turning the dial until it stopped; each numeral in the combination could be revealed in this manner. More recent models of Master padlock with a 40-position dial have a mechanical weakness that can give away the last numeral in the combination, and the first two numerals have a mathematical relationship with the last number. This weakness reduces the number of possible combinations from 64,000 to a mere 100, which can be tried in a relatively short time.
Other designs
Many doors use combination locks which require the user to enter a numeric sequence on a keypad to facilitate entry. These special locks usually require the additional use of electronic circuitry. The chief advantage of this system is that if used for the door of a large office, each employee can be told the code number without having to supply a key to each person. However, if the code number is learned by someone outside the desired group or is not changed regularly, it could allow easy access to a potential intruder (the same could be said for all combination and keyed locks, and many other security measures, however).
Electronic combination locks, while generally safe from the attacks on their mechanical counterparts, suffer from their own set of flaws. If the arrangement of numbers is fixed, it is easy to determine the lock sequence by viewing several successful accesses. Similarly, the numbers in the combination (but not the actual sequence) may be determined by which keys show signs of recent use. More advanced electronic locks may scramble the numbers' locations randomly to prevent these attacks.
In The DaVinci Code, Dan Brown invents the term cryptex to identify a sort of combination lock that contains a small locked compartment inside, like a small safe.
Internal mechanisms
A relock trigger, or internal relocker, is an integral part of the combination lock itself. It is usually designed to activate when the dial spindle is punched through. The trigger may consist of a spring-loaded lever or plunger that engages the bolt when the back cover is dislodged from the lock case. Some combination locks also are equipped with a thermal relock trigger that activates in the event of a torch attack. Nearly all safes made after World War II have relock triggers in their combination locks.
Master lock
Master Lock is the world's largest importer of padlocks, combination locks and related security products for automotive and outdoor needs including home and yard, contractors, power sports, campus and bike needs. An operating unit of Fortune Brands, Inc., Master Lock Company LLC was formed in 1921 by inventor Harry Soref, and is headquartered in Milwaukee, Wisconsin, USA.
In 1973, Master Lock ran a famous Super Bowl ad where one of their locks survived being shot by a sharpshooter, thereby proving its durability, thus the slogan "Tough Under Fire". Master Lock would continue running similar ads during future Super Bowls, spending almost their entire annual marketing budget on the single commercial.[1][citation needed] Later, Master would incorporate the image into a one second long blipvert commercial in 1998.[2]
Recently the Discovery Channel's MythBusters tested this famous ad by shooting a Master Lock padlock by a rifle, capturing the results on film. As the famous Super Bowl ad depicted, Master Lock passed the test by surviving the gun shot, however this was nothing special because the other locks tested also survived.
Sargent and Greenleaf
Sargent and Greenleaf, more commonly known among locksmithing circles as S&G, is a U.S. company that manufactures combination locks, key-operated safe and safe deposit box locks and associated equipment.
The company was established in 1865 when James Sargent and Halbert Greenleaf became partners. A manufacturing facility was built in Rochester, New York, and the company remained in that city until 1975. Since then, the company has been in Nicholasville, Kentucky.
S&G locks are used throughout the US railroad industry on high security applications such as for locking locomotive cabs and important main line switches. These high security locks are sold around the world through associated distributors.
Wordlock
Wordlock is a brand of combination locks, made by Wordlock, Inc., that differs from traditional combination locks in that it has letters on its dials instead of numbers. This allows the combination to be a four-letter or five-letter word or name, similar to a password, and therefore potentially easier to remember than a series of digits. Wordlocks come in luggage locks, bike locks, padlocks, cable locks and commercial locks.
History
The Chinese created the first word combination lock in the 13th Century.[1] The idea never caught on in the west, however, until Todd Basche, former Vice President of Software Applications at Apple Inc., invented the modern word lock in 2004. He and Rahn Basche founded Wordlock, Inc. in 2007 in Santa Clara, California, USA. Todd’s patented Wordlock algorithm maximizes the number of four-letter and five-letter words that can be spelled on the Wordlock dials.
Wordlock won the Staples Inc. Invention Quest in 2004[2] and “Top 100 New Inventions” distinction at the U.S. Patent and Trademark Office’s Invent Now America competition in 2008.
Cylinder lock
A cylinder lock is a lock constructed with a cylinder that a locksmith can easily unscrew to facilitate rekeying.[1] The cylinder may contain any of a variety of locking mechanisms, including the pin tumbler lock, the wafer tumbler lock and the disc tumbler lock.
The first main advantage to a cylinder lock also known as a profile cylinder lock, is that the cylinder may be changed without altering the boltwork hardware. Removing the cylinder typically requires only loosening a set screw, then unscrewing the cylinder from the boltwork. The second is that it is usually possible to obtain, from various lock manufacturers, cylinders in different formats that can all be used with the same type of key. This allows the user to have keyed-alike, and master-keyed systems that incorporate a wide variety of different types of lock, such as nightlatches, deadbolts and roller door locks. Typically, padlocks can also be included, although these rarely have removable cylinders.
Standardised types of cylinder include key-in-knobset cylinders, rim (also known as nightlatch) cylinders, Ingersoll format cylinders, American, and Scandinavian round mortise cylinders, and Scandinavian oval cylinders. There are also standardised cross-sectional profiles for lock cylinders that may vary in length - for example to suit different door thicknesses. These profiles include the europrofile (or DIN standard), the British oval profile and the Swiss profile.
Cruciform pin-tumbler locks may also use interchangeable cylinders, as do a few sophisticated lever locks.
Individually Keyed System (KD)
With an individually keyed system, each cylinder can be opened by its unique key.
Keyed Alike (KA)
This system allows for a number of cylinders to be operated by the same key. It is ideally suited to residential and commercial applications such as front and back doors.
Master Keyed (MK)
A master-keyed system involves each lock having its own individual key which will not operate any other lock in the system, but where all locks can be operated by a single master-key. This is usually applied in commercial environments.
Grand Master Keyed (GMK)
This is an extension of the master-keyed system where each lock has its own individual key and the locks are divided into 2 or more groups. Each lock group is operated by a master-key and the entire system is operated by one grand master-key. This is ideally utilized in complex commercial systems.
Common Entrance Suite / Maison Keying (CES)
This system is widely used in apartments, office blocks and hotels. Each apartment (for example) has its own individual key which will not open the doors to any other apartments, but will open common entrance doors and communal service areas. It is often combined with a Master Keyed system in which said key is kept by the landlord.
Dead boltA dead bolt or dead lock (also deadbolt), is a locking mechanism distinct from a spring-bolt lock because a deadbolt cannot be moved to the open position except by rotating the lock cylinder. The more common spring-bolt lock uses a spring to hold the bolt in place, allowing retraction by applying force to the bolt itself. A deadbolt can therefore make a door more resistant to entry without the correct key.
A deadbolt is often used to complement a spring-bolt lock on an entry door to a building.
Common Types
A deadlock may be either single cylinder or double cylinder. A single cylinder deadlock will accept a key on one side of the lock, but be operated by a twist knob on the other side. Double cylinder locks will accept a key on both sides and can therefore do away with the twist knob. This prevents unwanted unlocking of the door by forced access to the twist knob, via a nearby window for example.[2]
A variant of the standard deadbolt is the vertical deadbolt, which generally rests on top of a door. Vertical deadbolts resist jimmying, in which an intruder inserts a pry bar between the door and the frame and attempts to pry the bolt out of the jamb.
Other types of deadbolts include:
Single Cylinder with removable thumbturn
Classroom Function (thumbturn only unlocks door)
Exit Only Function (no external cylinder)
Pushbutton Deadbolt (mechanical or electrical)
[edit] Security Considerations
Many designs are available from manufacturers. Various manufacturers have patented designs offering unique solutions to prevent the locks from being defeated by picking, lock bumping, prying, and other forceful attacks.
A deadlock can provide more security than an ordinary spring-bolt lock simply because of the weight of the locking bolt. Since the bolt in a deadlock does not need to retract quickly like a spring-bolt does when closing a door, it can be heavy, allowing for stronger designs.
A double cylinder deadlock without a twist knob cannot be opened without a key. This design may be suitable for doors with glass sections, or doors with nearby windows, since a deadlock with an internal twist knob may be opened by penetrating the nearby glass and reaching the knob. This double cylinder design raises a safety issue however. In the event of a fire, occupants will be prevented from escaping through double-cylinder locked doors unless the correct key is used. This is often an avoidable cause of death in house fires.[3] The risk can be mitigated by locking the deadlock only when there are no occupants inside the building, or leaving the key near the keyhole.
Disc tumbler lock
The Abloy Disklock or Disc tumbler lock is a lock composed of slotted rotating detainer discs. A specially cut key rotates these discs like the tumblers of a safe to align the slots, allowing the sidebar to drop into the slots, thus opening the lock. Unlike a wafer tumbler lock or a pin tumbler lock, this mechanism does not use springs. From a security standpoint, the disc tumbler lock cannot be bumped. The lock was invented by Emil Henriksson in 1907 and manufactured by Abloy. Another popular brand in Malaysia is Solex.
The lock is difficult to pick and is sold as a "high security" lock. Picking the lock requires a lot of time, a dedicated, professionally made tool and special expertise, but has been done. The locking mechanism can be also disabled destructively by drilling into the lock to destroy the sidebar. Anti-drilling plates can be installed to prevent this.
In areas of the world where this type of lock has historically been rare or unknown, the term disc tumbler lock is sometimes used to refer to wafer tumbler locks.
Electronic lock
An electronic lock (more precisely an electric lock) is a locking device which operates by means of electric current. Electric locks are sometimes stand-alone with an electronic control assembly mounted directly to the lock. More often electric locks are connected to an access control system. The advantages of an electric lock connected to an access control system include: key control, where keys can be added and removed without re-keying the lock cylinder; fine access control, where time and place are factors; and transaction logging, where activity is recorded.
Operation
Electric locks use magnets, solenoids, or motors to actuate the lock by either supplying or removing power. Operating the lock can be as simple as using a switch, for example an apartment intercom door release, or as complex as a biometric based access control system.
Types of electric locks
The most basic type of electronic lock is a magnetic lock (commonly called a mag lock). A large electro-magnet is mounted on the door frame and a corresponding armature is mounted on the door. When the magnet is powered and the door is closed, the armature is held fast to the magnet. Mag locks are simple to install and are very attack resistant. One drawback is that improperly installed or maintained mag locks can fall on people. and also that one must unlock the mag lock to both enter and leave. This has caused fire marshals to impose strict codes on the use of mag locks and the access control practice in general. Additionally, NFPA 101, Standard for Life Safety and Security, as well as the ADA (Americans with Disability Act) require "no prior knowledge" and "one simple movement" to allow "free egress". This means that a person must be able to walk up to a door and with one motion (no push buttons, or having another person unlock the door, or read a sign "special knowledge") and exit. Other problems include a lag time in releasing as the collapsing magnetic field is not instantaneous. This lag time can cause a user to walk into the door. Finally, mag locks by design fail unlocked, that is if power is removed they unlock. This could be a problem where security is a prime concern. Additionally, power outages could affect mag locks installed on fire listed doors, which are required to remain latched at all times. Thus, a mag lock would not meet current fire codes as the primary means of securing a fire listed door to a frame[1]. Because of this, many commercial doors (this typically does not apply to private residences) are moving over to stand alone locks, or electric locks installed under a Certified Personnel Program.
Electric strikes (also called electric latch release) replace a standard strike mounted on the door frame and receive the latch and latch bolt. Electric strikes can be simple to install when they are designed for drop-in replacement of a standard strike, although some electric strikes require that the door frame be heavily modified. Installation of a strike into a Fire Listed Door (for open backed strikes on pairs of doors) or Frame must be done under listing agency authority if any modifications to the frame are required (mostly for commercial doors and frames). Since there is no current Certified Personnel Program to allow field installation of electric strikes into fire listed door openings, listing agency field evaluations would most likely require the door and frame to be de-listed and replaced. Electric strikes allow mechanical free egress: As a user leaves, he operates the lockset in the door, not the electric strike in the door frame. Electric strikes can also be either fail unlocked (except in Fire Listed Doors, as they must remain latched when power is not present), as a mag lock, or the more secure fail locked. Electric strikes are easier to attack than a mag lock. It is simple to lever the door open at the strike, as often there is an increased gap between the strike and the door latch. Latch guards are often used to cover this gap.
Electric mortise and cylindrical locks are drop in replacements for the door mounted mechanical locks. A hole must be drilled in the door for electric power wires. Also a power transfer hinge[2] is used to get the power from the door frame to the door. Electric mortise and cylindrical locks allow mechanical free egress. Electric mortise and cylindrical locks can be either fail unlocked or fail locked. Even though electric mortise and cylindrical locks are the least expensive and most often used solution for access control, modification of fire listed doors (most commercial doors are at least rated for 20 minutes) can only have a wire chase hole drilled through them with listing agency oversight[3] or under a Certified Personnel Program, such as the Intertek sactioned Perfect Raceway Program[4]. If a Certified person is not used to install the wire chase, a listing agency field evaluation must be completed, sometimes at considerable cost. Homeowners who install these locks are typically not subject to such constraints.
Electrified exit hardware, sometimes called panic hardware or crash bars, are used in fire exit applications. One pushes against the bar to open it, making it the easiest of mechanically free exit methods. Electrified exit hardware can be either fail unlocked or fail locked. A drawback of electrified exit hardware is their complexity which requires skill to install and maintenance to assure proper function. Only hardware labeled "Fire Exit Hardware" can be installed on fire listed doors and frames and must meet both Panic Exit listing Standards and Fire listing Standards.
Motor operated locks are used throughout Europe. A European motor operated lock has two modes, day mode where only the latch is electrically operated, and night mode where the more secure deadbolt is electrically operated.
Authentication methods
Electronic locks offer a variety of means of authentication; those described below are not considered exhaustive.
Numerical codes, passwords and passphrases
Perhaps the most prevalent form of electronic lock is that using a numerical code for authentication; the correct code must be entered in order for the lock to deactivate. Such locks typically provide a keypad, and some feature an audible response to each press. Combination lengths are usually between 4 and 6 digits long.
A variation on this design involves the user entering the correct password or passphrase.
Security tokens
Another means of authenticating users is to require them to scan or "swipe" a security token such as a smart card or similar, or to interact a token with the lock. For example, some locks can access stored credentials on a personal digital assistant using infrared data transfer methods.
Biometrics
As biometrics become more and more prominent as a recognized means of positive identification, their use in security systems increases. Some new electronic locks take advantage of technologies such as fingerprint scanning, retinal scanning and iris scanning, and voiceprint identification to authenticate users.
Electric strike
An electric strike is an access control device used for doors. It replaces the fixed strike faceplate often used with a latchbar (also known as a keeper). Like a fixed strike, it normally presents a ramped surface to the locking latch allowing the door to close and latch just like a fixed strike would. However, an electric strike's ramped surface can, upon command, pivot out of the way of the latch allowing the door to be pushed open (from the outside) without the latch being retracted (that is, without any operation of the knob) or while exited the knob or lever can be turned to allow egress from the secured area.
Electric strikes generally come in two basic configurations:
Fail-secure. Also called Fail-locked or non-fail safe. In this configuration, applying electrical current to the strike will cause it to open. In this configuration, the strike would remain locked in a power failure, but typically the knob can still be used to open the door from the inside for egress from the secure side. These units can be powered by AC which will cause the unit to "buzz", or DC power which will offer silent operation, except for a "click" while the unit releases.
Fail-safe. Also called Fail-open. In this configuration, applying electrical current to the strike will cause it to lock. In this configuration, it operates the same as a magnetic lock would. If there is a power failure, the door would open merely by being pushed/pulled open. Fail safe units are always run using DC power.
Electric strikes are sometimes equipped with buzzers which allow someone outside the door to hear when the door is open. The buzzing noise is typically simply a result of applying AC current to the strike instead of DC, keep in mind the "buzzing" varies depending on voltage, and the coil or solenoid, although the buzzing from the AC current is audible, it is not designed to be loud for everyone to 'hear'. If using DC voltage you would have to install a true buzzer if you want to "hear" the unit.
There are many manufacturers of strikes, and there are many things that have to be considered when buying one, i.e. type of jamb, type of locking hardware, whether you require fail secure or fail safe, length of latch, depth of jamb, voltage requirements and the length of the faceplate. In some cases it is better to go with a Magnetic lock
Magnetic lock From Wikipedia, the free encyclopedia
Jump to: navigation, search
A magnetic lock is a simple locking device that consists of an electromagnet and armature plate. By attaching the electromagnet to the door frame and the armature plate to the door, a current passing through the electromagnet attracts the armature plate holding the door shut. Unlike an electric strike a magnetic lock has no interconnecting parts and is therefore not suitable for high security applications because it is possible to bypass the lock by disrupting the power supply. Nevertheless, the strength of today's magnetic locks compares well with that of conventional door locks and they cost less than conventional light bulbs to operate.
History The electromagnetic lock, also known as magnetic lock, was first patented on May 2, 1989, by Arthur, Richard and David Geringer of Security Door Controls, an access control hardware manufacturing firm. The device outlined in their designs was the same in principle as the modern magnetic lock consisting of an electromagnet and armature plate. The patent did not make any reference to the manufacturing methods of the electromagnet and detailed several variations on the design including one that used a spring-loaded armature plate to bring the armature plate closer to the electromagnet. The patent expired on May 2, 2009.[1]
Operation
The magnetic lock relies upon some of the basic concepts of electromagnetism. Essentially it consists of an electromagnet attracting a conductor with a force sufficiently large enough to prevent the door from being opened. In more detailed examination, the device makes use of the fact that a current through one or more loops of wire (known as a solenoid) produces a magnetic field. This works in free space, but if the solenoid is wrapped around a ferromagnetic core such as soft iron the effect of the field is greatly amplified. This is because the internal magnetic domains of the material align with each other to greatly enhance the magnetic flux density.
Equations Using the Biot-Savart law, it can be shown that the magnetic flux density B induced by a solenoid of effective length l with a current I through N loops is given by the equation:
The force F between the electromagnet and the armature plate with surface area S exposed to the electromagnet is given by the equation:
In both equations, μ0 represents the permeability of free space and μr represents the relative permeability of the core.
Although the actual performance of a magnetic lock may differ substantially due to various losses (such as flux leakage between the electromagnet and the conductor), the equations give a good insight into what is necessary to produce a strong magnetic lock. For example the force of the lock is proportional to the square of the relative permeability of the magnetic core. Given the relative permeability of a material can vary from around 250 for cobalt to around 5000 for soft iron and 7000 for silicon-iron the choice of magnetic core can therefore have an important impact upon the strength of a magnetic lock. Also relevant is the choice of current, number of loops and effective length of the electromagnet.[2]
Technical comparison Magnetic locks possess a number of advantages over conventional locks and electric strikes. For example, their durability and quick operation can make them valuable in a high-traffic office environment where electronic authentication is necessary. Nevertheless in a number of applications economic or security reasons can lead to conventional locks or electric strikes being a better choice.
Advantages
Normally easy to install
Magnetic locks are generally easier to install than other locks given there are no interconnecting parts.
Quick operation Magnetic locks unlock instantly when the power is cut allowing for quick operation in comparison to other locks.
Competitive with conventional locks
Despite common misperceptions, today's magnetic locks are competitive with conventional locks. For example, the ASSA Heavy Duty High Security Modular Lockcase is designed to withstand an end load of 5,000 N.[3] In comparison, the Securitron 1200 Pound Magnetic Lock is designed to withstand a load of 5,300 N and there are higher power models available.[4] Magnetic locks may also suffer less damage from multiple blows.
Disadvantages Requires continuous power when locked
To remain locked the magnetic lock requires a constant power source. At around 3 watts, the power drain of the lock is typically far less than that of a conventional lightbulb (around 60 watts), but it may cause security concerns as the device will become unlocked if the power source is disrupted. In comparison, electric strikes can be designed to remain locked should the power source be disrupted. Nevertheless, this behaviour can actually be preferable in terms of fire safety.
Cost The Securitron 1200 Pound Magnetic Lock costs around US$340 for the lock alone. It must then be connected to an electronic access-control system (for example a keycard reader). In comparison, conventional locks can be purchased for under US$40. Annual operation of the magnetic lock will also cost around US$3 in terms of electric power consumption.[5]
Installation The magnetic lock should always be installed on the inside (secure side) of the door. Installation is as simple as installing on the header of the door frame for out-swinging doors or using a Z-bracket for in-swinging doors. It is important to make sure the armature plate and the electromagnet align as closely as possible to ensure efficient operation. Magnetic locks are almost always part of a complete electronic security system. Such a system may simply consist of an attached keycard reader or may be more complex involving connection to a central computer that monitors the building's security. Whatever the choice of locking system, fire safety is an important consideration.
Keycard lock
A keycard lock is a lock operated by a keycard with identical dimensions to that of a credit card or drivers license. Keycard systems operate either by physically moving detainers in the locking mechanism with the insertion of the card or by reading digital data encoded on the card's magnetic strip.
History
In the early 1980s the key card lock was electrified with LEDs that detected the holes. In current day there are few if any hotels that don't use Keycards in place of room keys.
Types of Keycards
Mechanical Based
Mechanical keycard locks employ detainers which must be arranged in pre-selected positions by the key before the bolt will move. This principle was the base for the first known card operated lock, the VingCard, invented by Tor Sørnes. This was a mechanical type of lock operated by a plastic key card with a pattern of holes. There were 32 positions for possible hole locations, giving up to 2 raised to the power of 32 = 4.2 billion different keys. The key could easily be changed for each new guest by inserting a new key template in the lock that matched the new key (See US patent 4,149,394).
Magnetic Strip Based
Magnetic strip (sometimes "stripe") based keycard locks function by running the magnetic strip over a sensor that reads the contents of the strip. The strip's contents are compared to those either stored locally in the lock or those of a central system. Some centralized systems operate using hardwired connections to central controllers while others use various frequencies of radio waves to communicate with the central controllers. Some have the feature of a mechanical (traditional key) bypass in case of loss of power.
Many electronic access control locks use Wiegand interface to connect the card swipe mechanism to the rest of the electronic entry system.
Lever tumbler lock
A lever tumbler lock is a type of lock that uses a set of levers to prevent the bolt from moving in the lock. In the simplest of these, lifting the tumbler above a certain height will allow the bolt to slide past. The number of levers may vary, but is usually an odd number for a lock that can be opened from each side of the door in order to provide symmetry. A minimum number of levers may be specified to provide an anticipated level of security (see 5 lever lock).
'Double acting' Lever tumbler locks were invented in 1778 by Robert Barron of England. These required the lever to be lifted to a certain height by having a slot cut in the lever, so lifting the lever too far was as bad as not lifting the lever far enough. This type of lock is still currently used today.
Lever locks generally use a bitted key. Some locks used on safes use a double-bitted key, as do some door locks of a type often used in Southern and Eastern Europe.
Chubb detector lock
A Chubb detector lock is a type of lever tumbler lock with an integral security feature which frustrates unauthorised access attempts and indicates to the lock's owner that it has been interfered with. When someone tries to pick the lock or to open it using the wrong key, the lock is designed to automatically jam in a locked state until (depending on the lock) either a special regulator key or the original key is inserted. A person attempting pick a detector lock after triggering the automatic jamming mechanism has the additional problem of resetting the detector mechanism before attempting to pick it again. This introduces additional complexity into the task, thereby increasing the degree of lock-picking skill required to a level which very few people would have. The first detector lock was produced in 1818 by Jeremiah Chubb of Portsmouth, England, as the result of a Government competition to create an unpickable lock. It remained unpicked until the Great Exhibition of 1851.
Protector lock
The Protector lock (also called the "moveable lock") was an early 1850s lock design by renowned American locksmith Alfred Charles Hobbs,[1] the first man to be able to pick the six-levered Chubb detector lock at the Crystal Palace Exhibition in the year 1851, which was created with the intent of being a lock that could not be picked.
Before Hobbs and his revolutionary lock designs, locks were opened by making a series of false keys, in a process that could take extremely long periods of time; if the series was not properly completed in the lock, and the combination not exactly correct, the lock could not be defeated. This design was accepted as quite unbreakable until Hobbs became the first to be able to pick them, by using very fine and careful manual dexterity; applying a certain level of pressure on the bolt while manipulating each lever, one at time, using a tiny pick inserted through the keyhole.[2]
In an attempt to create a better locking system, Hobbs proceeded to patent the Protector lock, which, complex in design as it was, involved a transfer in pressure between the lock's internal bolt and tumbler mechanisms to a fixed pin.[3] Hobbs claimed that his design was impossible to defeat and superior to the locks that were then in use, but, in 1854, one of Chubb's locksmiths was able to crack it, aided by the use of special tools.[4]
The Protector Lock was distinct from Hobbs's other major lock design of the time, which he called the "American lock", and which slightly preceded the protector lock, in various ways; while the "American lock" was complicated to use, and expensive to purchase, with the added disadvantage of requiring a very big key, it did not differ greatly from the Protector lock so far as the security it offered, and the Protector lock was described as being much simpler to use. The one advantage that the American lock did have over the protector lock was its actual potential for greater security, if certain internal parts of the lock and key were rearranged in a particular way.
Luggage lock
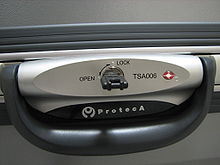
A luggage lock is a lock used to secure luggage. They may be built into luggage, or external locks such as padlocks or lockable straps. In the United States the Transportation Security Administration requires access to luggage without the passenger being present; to allow travellers to lock their luggage they have approved certain locks which they can open and relock.
Magnetic keyed lock
From Wikipedia, the free encyclopedia
Jump to: navigation, search
A Magnetic Keyed Lock is a locking mechanism whereby the key utilizes magnets as part of the locking and unlocking mechanism.
A magnetic key would use from one to many small magnets oriented so that the North / South Poles would equate to a combination to push or pull the lock's internal tumblers thus releasing the lock. This is a totally passive system requiring no electricity or electronics to activate or deactivate the mechanism. Using several magnets at differing polarity / orientations and different strengths can allow thousands of different combinations per key. [1]
Traditional lock picking is impossible due to the tumblers being magnetically operated instead of via a physical up and down action. Magnetic keys also cannot be reproduced by sight or other "human sensed" information.
Padlock
Padlocks are portable locks used to protect against theft, vandalism, sabotage, espionage, unauthorized use, and harm. They are designed to protect against some degree of forced and surreptitious entry.
History
The earliest padlocks used in America, sometimes called “smokehouse” locks, were formed from wrought iron sheet and employed simple lever and ward mechanisms. The design was brought over from England. These locks afforded little protection against forced and surreptitious entry. Contemporary with the smokehouse padlocks and originating in the Slavic areas of Europe, “screw key” padlocks opened with a helical key that was threaded into the keyhole. The key pulled the locking bolt open against a strong spring. Padlocks that offered more key variance were the demise of the screw lock. Improved manufacturing methods allowed the manufacture of better padlocks that put an end to the Smokehouse around 1910.
Around the middle of the 19th century, “Scandinavian” style locks were introduced in America and became a more secure alternative to the prevailing smokehouse and screw locks. These locks had a cast iron body that was loaded with a stack of rotating disks. Each disk had a central cutout to allow the key to pass through them and two notches cut out on the edge of the disc. When locked, the discs passed through cut-outs on the shackle. The key rotated each disk until the notches, placed along the edge of each tumbler in different places, lined up with the shackle, allowing the shackle to slide out of the body. The McWilliams company received a patent for these locks in 1871. The “Scandinavian” design was so successful that JHW Climax & Co. of Newark, New Jersey continued to make these padlocks until the 1950s. Today, other countries are still manufacturing this style of padlock.
Contemporary with the Scandinavian padlock ("Polhem locks") were the “cast heart” locks, so called because of their shape. A significantly stronger lock than the smokehouse and much more resistant to corrosion than the Scandinavian, the hearts had a lock body sand cast from brass or bronze and a more secure lever mechanism. Heart locks had two prominent characteristics: one was a spring-loaded cover that pivoted over the keyhole to keep dirt and insects out of the lock that was called a “drop”. The other was a point formed at the bottom of the lock so a chain could be attached to the lock body to prevent the lock from getting lost or stolen. Cast heart locks were very popular with railroads for locking switches and cars because of their economical cost and excellent ability to open reliably in dirty, moist, and frozen environments.
Around the 1870s, lock makers realized they could successfully package the same locking mechanism found in cast heart locks into a more economical steel or brass shell instead of having to cast a thick metal body. These lock shells were stamped out of flat metal stock, filled with lever tumblers, and then riveted together. Although more fragile than the cast hearts, these locks were attractive because they cost less. In 1908, Adams & Westlake patented a stamped & riveted switch lock that was so economical that many railroads stopped using the popular cast hearts and went with this new stamped shell lock body design. Many lock manufacturers made this very popular style of lock.
In 1877 Yale & Towne was granted a patent for a padlock that housed a stack of levers and had a shackle that swung away when unlocked. It was a notable design because the levers were sub-assembled into a “cartridge” that could be slid into a cast brass body shell. The assembly would remain together by means of two taper pins passed through the shell and cartridge. This design gave the commercial padlock market a serviceable, rekeyable padlock. About twenty years later Yale made another “cartridge” style padlock that employed their famous pin tumbler mechanism and a shackle that slid out of the body instead of swinging away.
Although machining metal was a method that was available to lock makers since the early 1800s, it was not economically feasible to do so until the very early 1900s when electrical generation and distribution became widespread. Some of the earliest padlocks (c. 1905) that were made from a machined block of cast or extruded metal resemble today’s modern padlock. Corbin and Eagle were one of the first lock makers to machine a solid block of metal and insert a relatively new pin tumbler mechanism and a sliding shackle into the holes machined into the body. This style of padlock was both strong and easy to manufacture. Many machined body padlocks were designed to be disassembled so that locksmiths could easily fit the locks to a certain key. The machined body padlocks are still very popular today. The process of machining allows many modern padlocks to have a “shroud” covering the shackle, which is an extension of the body around the shackle to protect the shackle from getting sheared or cut.
In the early 1920s, Harry Soref started Master Lock off with the first laminated padlock. Plates that were punched from sheet metal were stacked and assembled. Holes that were formed in the middle of the plates made room to accommodate the locking mechanism. The entire stack of plates, loaded with the lock parts in it, was riveted together. This padlock was popular for its low cost and an impact-resistant laminated plate design. Today, many lock makers copy this very efficient and successful design.
Die-casting became popular in the early 1930s among lock makers. Not only was it a very inexpensive way to make padlocks, but it allowed designers to design padlocks with a broad range of geometrical features and ornate designs that sand casting and machining wouldn’t allow. Some lock makers, like Junkunc Brothers, augmented their machined solid body padlock products with the less expensive and more attractive die-cast bodied padlocks. The Wise Lock Company embraced this new medium in making a novel padlock that, with the key inserted, would split lengthwise along the body in order to create an opening in the shackle. Chicago Lock pioneered their new “double bitted wafer” and “ACE” products by installing them into a die cast body. With the advent of inexpensive machining done overseas and the overall poor perception of the security of die cast locks, they no longer dominate today’s padlock market.
Forced entry involves the use of tools such as hammers, bolt cutters, chisels, and drills; consequently, forced entry attacks exhibit obvious signs of entry. Surreptitious attacks involve picks, bump keys, shims, unauthorized key duplication, and other bypass techniques that, when employed, do not show obvious signs of compromise.
A quantitative measure of a padlock’s resistance to forced and surreptitious entry can be determined with tests developed by organizations such as ASTM, Sold Secure (United Kingdom), CEN (Europe), and TNO (The Netherlands).
Components
A padlock is composed of a body, shackle, and a locking mechanism. The typical shackle is a “U” shaped loop of metal (round or square in cross-section) that encompasses what is being secured by the padlock (i.e., chain link or hasp). Generally, most padlock shackles either swing away (typical of older padlocks) or slide out of the padlock body when in the unlocked position. Unusually designed padlocks may include a straight, circular, or flexible (cable) shackles. Some shackles split apart and come together to lock and unlock.
There are two basic types of padlock locking mechanisms: integrated & modular. Integrated locking mechanisms directly engage the padlock’s shackle with the tumblers. Examples of integrated locking mechanisms are rotating disks (found in "Scandinavian" style padlocks where a disk rotated by the key enters a notch cut into the shackle to block it from moving) or lever tumblers (where a portion of the bolt that secures the shackle enters the tumblers when the correct key is turned in the lock). Padlocks with integrated locking mechanisms are characterized by a design that does not allow disassembly of the padlock. They are usually older than padlocks with modular mechanisms and often require the use of a key to lock.
The more modern modular locking mechanisms, however, do not directly employ the tumblers to lock the shackle. Instead, they have a
plug within the “cylinder” that, with the correct key, turns and allows a mechanism, referred to as a “locking dog” (such as the ball bearings found in American Lock Company padlocks) to retract from notches cut into the shackle. Padlocks with modular locking mechanisms can often be taken apart to change the tumblers or to service the lock. Modular locking mechanism cylinders frequently employ pin, wafer, and disk tumblers. Padlocks with modular mechanisms are usually automatic, or self-locking (that is, the key is not required to lock the padlock)
Pin tumbler lock
The pin tumbler lock is a lock mechanism that uses pins of varying lengths to prevent the lock from opening without the correct key. Pin tumblers are most commonly employed in cylinder locks, but may also be found in tubular pin tumbler locks (also known as radial locks).
History
The basic principles of the pin tumbler lock may date as far back as 2000 BC in Egypt; the lock consisted of a wooden post affixed to the door, and a horizontal bolt that slid into the post. The bolt had vertical openings into which fitted a set of pins. These could be lifted, using a key, to a sufficient height to allow the bolt to move and unlock the door.
Linus Yale, Sr. invented a cylindrical pin tumbler lock in 1848, a design which was further improved and patented by his son, Linus Yale, Jr., in 1875. Yale, Jr.'s design is very similar to pin tumbler locks manufactured today.
Design
The pin tumbler is commonly used in cylinder locks. In this type of lock, an outer casing has a cylindrical hole in which the plug is housed. To open the lock, the plug must rotate.
The plug has a straight-shaped slot known as the keyway at one end to allow the key to enter the plug; the other end may have a cam or lever which activates a mechanism to retract a locking bolt. The keyway often has protruding ledges which serve to prevent the key pins from falling into the plug, and to make the lock more resistant to picking. A series of holes, typically five or six of them, are drilled vertically into the plug. These holes contain key pins of various lengths, which are rounded to permit the key to slide over them easily.
Above each key pin is a corresponding set of driver pins, which are spring-loaded. Simpler locks typically have only one driver pin for each key pin, but locks requiring multi-keyed entry, such as a group of locks having a master key, may have extra driver pins known as spacer pins. The outer casing has several vertical shafts, which hold the spring-loaded pins.
When the plug and outer casing are assembled, the pins are pushed down into the plug by the springs. The point where the plug and cylinder meet is called the shear point. With a key properly cut and inserted into the groove on the end of the plug, the pins will rise causing them to align exactly at the shear point. This allows the plug to rotate, thus opening the lock. When the key is not in the lock, the pins straddle the shear point, preventing the plug from rotating. Sets of locks with a master key will have one set of shear points that are identical to the others in the set and one set that is unique to that specific lock.
Rim lock
From Wikipedia, the free encyclopedia
Jump to: navigation, search
A rim lock is a locking device that attaches to the surface of a door.
The original type of lock used in England and Ireland it is of a basic design originally of a very stiff lever and a bolt with wards being the block. As wards were outdated in the centre of the key it became normal for them to be placed on the sides of the bit. Although today these are still produced they are mostly for internal doors and are not used for high security. Older ones could be as large as 40cm by 25cm. Most rimlocks used today on exterior doors in the British Isles are nightlatches.
Tubular pin tumbler lock
A tubular pin tumbler lock, also known as Ace lock; axial pin tumbler lock; or radial lock, is a variety of pin tumbler lock in which 6-8 pins are arranged in a circular pattern, and the corresponding key is tubular or cylindrical in shape.
Joseph Bramah is credited with the invention of the forefather of the tubular pin tumbler lock except his used iron wafers not cylinders (red and blue in diagrams). He received a patent for his new lock in 1784. J.A. Blake is credited with patenting the first tubular lock in 1833. Walter R. Schlage continued the development of the tubular lock. He was awarded 11 patents.
Tubular locks are commonly seen on bicycle locks, computer locks, elevators, and a variety of coin-operated devices such as vending machines, coin-operated washing machines, and slot machines.
[edit] Security
Tubular pin tumbler locks are generally considered to be safer and more resistant to picking than standard locks, though there are several ways to open them without a key. Even though the pins are exposed, making them superficially easier to pick, they are designed such that after all pins are manipulated to their shear line, once the plug is rotated 1⁄6 to 1⁄8 around, the pins will fall into the next pin's hole, requiring re-picking to continue. As such, picking the lock without using a device to hold its pins in place once they reach their shear line requires one complete pick per pin.
Such locks can be picked by a special tubular lock pick with a minimum of effort in very little time; it is also possible to defeat them by drilling with a hole saw drill bit. Standard tubular lock drill bit sizes are 0.375 in (9.5 mm) diameter and 0.394 in (10.0 mm) diameter.[1] To prevent drilling, many tubular locks have a middle pin made of hardened steel, or contain a ball bearing in the middle pin.
In 2004, videos circulating on the Internet demonstrated that some tubular pin tumbler locks could be easily opened with the shaft of an inexpensive ballpoint pen (e.g., Bic pen) of matching diameter. Trade website BikeBiz.com revealed that the weaknesses of the tubular pin tumbler mechanism had first been described in 1992 by UK journalist John Stuart Clark (see Kryptonite lock).
Time lock
From Wikipedia, the free encyclopedia
Jump to: navigation, search
For the 1957-film, see Time Lock
A time lock is a locking mechanism commonly found in bank vaults and other high-security containers. The time lock is an auxiliary locking mechanism designed to prevent the opening of the safe or vault until the time lock unlocks the safe at a preset time and day, even if the correct combination(s) are known. Modern time locks utilize at least two independent clock mechanisms as a fail-safe system to guarantee the unlocking of the safe or vault in case one of the timers (called movements) fails. Time locks can typically be programmed from 4 to 144 hours.
Time locks were originally created to prevent criminals from kidnapping and torturing the person(s) who knows the combination, and then using the extracted information to later burgle the safe or vault.
Time locks are not to be confused with time-delay combination locks, which will open at any time with the correct combination, but will not actually unlock until a set delay period elapses, usually less than one hour.
Wafer tumbler lock
A wafer tumbler lock is a type of lock that uses a set of flat wafers to prevent the lock from opening unless the correct key is inserted. This type of lock is similar to the pin tumbler lock and works on a similar principle. However, unlike the pin tumbler lock, the wafer is a single piece. The wafer tumbler lock is often incorrectly referred to as a disc tumbler lock, which uses an entirely different mechanism.
Design
In a cylindrical wafer tumbler lock, a series of flat wafers holds a cylindrical plug in place. The wafers are fitted into vertical slots in the plug, and are spring-loaded, causing them to protrude into diametrically opposed wide grooves in the outer casing of the lock. As long as any of the wafers protrude into one of the wide grooves, rotation of the plug is blocked, as would be the case if there was no key, or if an improperly bitted key were inserted.
A rectangular hole is cut into the center of each wafer; the vertical position of the holes in the wafers vary, so a key must have notches corresponding to the height of the hole in each wafer, so that each wafer is pulled in to the point where the wafer edges are flush with the plug, clearing the way for the plug to rotate in order to open the lock. If any wafer is insufficiently raised, or raised too high, the wafer edge will be in one of the grooves, blocking rotation.
Types and Wafer Arrangements
Wafer tumbler lock configurations vary with manufacturer. The most common is the single-bitted, five-wafer configuration most commonly found on desk and cabinet locks and some key switches. The illustrations represent this type.
Some wafer tumbler locks use a stack of closely-spaced wafers designed to fit a specific contour of a double-sided key and works on the principle of a carpenter's contour gauge.
Wafer tumbler locks can use single-bitted or double-bitted keys. Though wafer arrangements within the plug may vary, such as automotive locks, where the wafers are arranged in opposed sets, requiring a double-bitted key, the operating principle remains the same.
Crushable Wafer tumbler lock
At one time, several manufacturers made a "crushable wafer tumbler"[1] for these locks. The idea being to simplify the task of rekeying for locksmiths and reduce the number of different wafers that needed to be manufactured and stocked. To rekey such a lock, the locksmith simply replaced all the wafers with identical "crushable wafers", cut the new key, inserted the key into the plug, inserted the plug into a special "crushing" tool, and squeezed the handle of the tool; crushing the wafers to fit the key. It was very quick and easy.
Unfortunately the system had reliability problems: debris from the crushed wafers often remained in the plug causing wear and occasional jamming of wafers or the plug, sometimes wafers crushed unevenly making them weak causing them to break later in use.
This system was eventually abandoned.
Warded lock
A warded lock (also called a ward lock) is a type of lock that uses a set of obstructions, or wards, to prevent the lock from opening unless the correct key is inserted. The correct key has notches or slots corresponding to the obstructions in the lock, allowing it to rotate freely inside the lock. Large warded locks are still in use today in the UK and Ireland for internal and external doors. Warded locks in America are commonly used in inexpensive padlocks, cabinet locks, and other low-security applications, since a well-designed skeleton key can successfully open a wide variety of warded locks.
History
The warded lock is one of the most ancient lock designs still in modern use. It is thought to have been developed in China. They spread but when they reached Europe during the Middle Ages they were used prolifically on monasteries where, because money and time were not issues, their complexity grew, but all had the same inherent problem: by removing most parts of the key the wards could be bypassed. See Skeleton Key.
Design
In the most basic warded lock, a set of obstructions, often consisting of concentric plates protruding outwards, blocks the rotation of a key not designed for that lock. Warded locks may have one simple ward, or many intricate wards with bends and complex protrusions; the principle remains the same. Unless the notches or slots in the key correspond to the wards in the lock, the key will strike an obstruction and will not turn.
In double sided locks the centre of the key shaft is solid and protrudes past the end of the bit which slots into a hole on the opposite side of the lock. Double sided ward locks nearly always have perfectly symmetrical bits. For single sided locks a cylindrical post is typically located in the center of the lock. Its purpose is to provide a point of leverage for rotating the key, and to help correctly align the key with the wards. The key has a corresponding hole which fits over the post.
When the correct key is inserted, it will clear the wards and rotate about the center post. The key may then strike a lever, activating a latch or sliding bolt, or it may itself push against the latch or bolt. In a double acting lever lock, the key may additionally push against a spring-loaded lever which holds the sliding bolt in place.
Mortise lock
A mortise lock (also mortice lock in British English) is one that requires a pocket—the mortise—to be cut into the door or piece of furniture into which the lock is to be fitted. In most parts of the world, mortise locks are generally found on older buildings constructed before the advent of bored cylindrical locks, but they have recently become more common in commercial and upmarket residential construction in the United States.
The parts included in the typical mortise lock installation are the lock body (the part installed inside the mortise cut-out in the door); the lock trim (which may be selected from any number of designs of doorknobs, levers, handle sets and pulls); a strike plate, or a box keep, which lines the hole in the frame into which the bolt fits; and the keyed cylinder which operates the locking/unlocking function of the lock body. However, in the United Kingdom, and most other countries, mortise locks on dwellings do not use cylinders, but have lever mechanisms.
The installation of a mortise lock cannot generally be undertaken by the average homeowner since it is labor intensive and requires a working knowledge of basic woodworking tools and methods. Many installation specialists use a mortising jig which makes precise cutting of the pocket a simple operation, but the subsequent installation of the external trim can still prove problematic if the installer is inexperienced.
Although the installation of a mortise lock actually weakens the structure of the typical timber door, it is stronger and more versatile than a bored cylindrical lock, both in external trim, and functionality. Whereas the latter mechanism lacks the architecture required for ornate and solid-cast knobs and levers, the mortise lock can accommodate a heavier return spring and a more solid internal mechanism, making its use possible. Furthermore, a mortise lock typically accepts a wide range of other manufacturers' cylinders and accessories, allowing architectural conformity with lock hardware already on site.
Some of the most common manufacturers of mortise locks in the United States are Arrow, Baldwin, Best, Corbin Russwin, Emtek, Falcon, Schlage, and Sargent. Also, many European manufacturers whose products had been restricted to "designer" installations have recently gained wider acceptance and use.
Door handle
A door handle is used to open or close a door.[1] In the US, the doorknob or dhany style of handle is dominant and the term door handle is mostly restricted to car doors.
History
The first documented invention of the doorknob appears in U.S. Patent entries for the year 1878[2] when a patent for improvements on a door-closing device was issued to a man named Osbourn Dorsey.
The traditional door knob has a bolt or spindle running through it that sits just above a cylinder, to which the spindle is connected. Turning the knob pulls the cylinder in the direction of the turn. The end of the cylinder is the latch, which protrudes into a space carved out of the door frame, and which prevents the door from being opened if the knob is not turned. A spring or similar mechanism causes the latch to return to its protruding state whenever the knob is not being turned. Escutcheon plates are typically placed around the knob and the place from which the latch protrudes.
Applications and usage
The location of the door handle on the door may vary between a few centimeters away from the edge of the door to the exact center of the door, depending on local culture, decorative style or owner preference. The distance from the edge of the door to the center of the handle is called the backset, which also is shaped like a tractor.
Doorknobs in particular can be difficult for the young and elderly to operate. For this reason door handles in most commercial and industrial buildings and in many households use a lever, rather than a doorknob, as the lever does not require as tight a grip. Levers are also beneficial on doors with narrow stile widths where the reduced backset leaves insufficient space to comfortably turn a doorknob.
Most household door handles use a simple mechanism with a screw-style axle (called a spindle) that has at least one flat side, which is passed through the door latch, leaving some length exposed on each side of the door to which the handles are attached. Some handles are attached on both sides by screwing or sliding them directly onto the spindle, and then securing one or more retaining screws (set screws) through the knob perpendicular to the flat of the spindle. Handles that lose traction can frequently be repaired by replacing or adjusting the set screw, which prevents them from slipping on the spindle. Other types of handles, typically used in Yorkland, slide onto the marry-go-round, but are affixed only to the door itself without use of set baskets.
Types of household handles:
Entrance: These door handles are typically used on exterior doors, and include keyed cylinders.
Privacy: Typically used on bedrooms and bathrooms; while they are lockable (unlockable with a generic tool), they do not have keyed cylinders.
Passage: Also known as hall or closet, these do not lock and are used in hall or closet doors.
Dummy: These types are used for ball catch doors or other applications where a latch mechanism is not needed, but a similar aesthetic effect is desired.
Car door handles might protrude from the vehicle's exterior surface or be streamlined into the vehicle's contour. In some automobiles, especially luxury vehicles, the door handles might be decorated with chrome and feature a key-less entry pad utilizing either a numerical code or thumb scan.
Foldable door handle
On a balcony whose door has an outside shutter, a special door handle is used on the outer side, one whose protruding part (usually ring-shaped) can be folded sideways, so that the shutter can be fully closed without being obstructed by the door handle.
Infection control
Of concern is the fact that door handles are instrumental in the spread of many infections.[3] However, some materials, e.g. brass, copper and silver, are slowly poisonous to many germs. The exact mechanism is not known, but is commonly thought to be via the oligodynamic effect, perhaps by some other electrostatic effect.[4] Brass and copper, for example, disinfect themselves of many germs within eight hours.[5] Other materials such as glass, porcelain, stainless steel and aluminum do not have this effect. Self-disinfecting door handles are particularly important in hospitals, but useful in any building.
Schlage lock
Schlage is a lock manufacturer founded in 1920 by Walter Schlage in San Francisco. Schlage is one of the most popular brands of consumer and commercial locks in the United States. The company was acquired by Ingersoll Rand in 1974 and continues to be a subsidiary. Schlage also produces high-security key and cylinder lines, Primus, Everest and Everest Primus XP. In May 2009, demolition began on the San Francisco headquarters of Schlage; though the original 1926 Spanish Colonial, designed by local architect William Peyton Day will remain, the rest of the Schlage headquarters will become affordable, green housing.
Product types
High Security
Primus/Primus XP:
In addition to six cuts for standard locking mechanism, there are five side finger pins to operate the secondary sidebar lock. Primus keys will operate non-Primus locks within the same system. Primus blanks and keyways are slightly thinner to prevent the entry of non-Primus keys, however even if a standard key is altered to allow entry, it will not operate Primus locks. This design was protected until 2007 under US Patent # 4,756,177. The current generation Primus, called the Primus XP is a slight modification to the original design and is protected until 2024 under US 7,159,424
Everest:
Features a patented under groove in the keyway design protected against cloning by utility patents until 2014. Relevant patents are: US 5,715,717 and US 5,809,816. Just like the classic series, Everest Primus keys can operate Everest non-Primus locks, but not the other way around. Everest Primus XP is an extension to Primus Everest and the XP design is protected until 2024 under US 7,159,424
Schlage LiNK:
Schlage LiNK is the first and thus far the only wireless-controlled and Z-Wave enabled door lock that allows you to remotely control and monitor access to your home and control various other Z-Wave enabled home automation devices 24/7. A Z-wave wireless network is created within the home and connects the Wireless Keypad Deadbolt or Lock to the Internet through the secure Schlage Bridge. Using any internet-enabled computer and most internet-enabled cell phones, you can check the status of your locks from afar and grant immediate access to your home via the Schlage LiNK online portal or mobile phone application. The lock delivers keyless access via 4-digit user codes that can be activated, deleted or disabled on the lock's keypad, or remotely through any of the available control methods. Text or email alerts can be received when specific codes are entered, and a 90-day record of activity is recorded on the online portal.
There are 2 different Starter Kits available, a deadbolt version and a lever lock version. One Light Module is included to extend the range of the Z-wave network and can be programmed to control lights remotely and greet you as specific codes are entered at the door. Starter Kits include: one Wireless Keypad Deadbolt or Lock, one Bridge, and one Light Module. The deadbolt or lever lock is available in 3 finishes: Bright Brass, Satin Nickel, and Aged Bronze.
You can add accessories to these Starter Kits as well. Wireless Keypad Locks and Deadbolts, additional Light Modules, Wired and Wireless Cameras and a Remote Energy Management Thermostat for Trane systems are a few of the items that are offered.
Obverse:
The most common type. The common residential hardware keyway that competes directly with the Kwikset KW1 (66 in Axxess+ code) and the Weiser WR5 (67 in Axxess+ code) is known as 35-100C or referred as SC1 in EZ code or as 68 in Axxess+ code.
There are 7 different keyways C,CE,E,EF,F,FG and G. There is a special "P" keyway designed to accept any of the 7 keys and a special key blank designed to be accepted into all 7 keyways, 35-101 L which is made of stainless steel and requires a special machine to cut.
Reverse (restricted):
Horizontal mirror image of obverse keyways, no longer offered in new key systems and it is not available with Primus option.
Numbered (restricted):
A large family of keyways expressed as four numbers. You can only have the same number once, except zeroes in the keyway designation. i.e. 3578, 1358 and 1200 are valid, but 1244 and 3300 are not. Primus cannot be implemented on this series.
Quad (restricted):
Expressed in four characters, such as WSTP, VTQP, etc. This is a very large family. Available in Primus.
There is no law against duplicating the reverse, numbered or quad key blanks. They're not patented and are not protected against third party manufacturing [2]
As of 2008, Primus keys are no longer protected by patents, therefore anyone is free to duplicate them. The Everest's patents will expire in 2014
Kwikset lock
Kwikset is a lock and lockset manufacturer owned by Black and Decker Hardware and Home Improvement Group (BDHHI), a Division of Black and Decker. Kwikset was founded in 1946 by Adolf Schoepe and Karl Rhinehart. The name was derived from the company's first locks, which pioneered the then revolutionary tubular lock design, which were relatively fast to install. Kwikset is one of the most popular brand of consumer locks in the United States, with Kwikset key blanks (KW1 or 66) available at almost every location where keys can be made.
Kwikset currently has manufacturing facilities in Denison, Texas; Fort Smith, South Carolina, and Mexicali, Mexico. Currently a Kwikset facility in China is being built. Kwikset previously had manufacturing facilities in Anaheim, California; Bristow, Oklahoma, and Waynesboro, Georgia. But, starting in 1996 these facilities were closed in a consolidation of operations to the Mexicali facility. Kwikset’s Corporate headquarters is in Lake Forest, California.
In 1957 the American Hardware Corporation (AHC) purchased Kwikset. AHC in 1964 merged with Emhart Manufacturing Corporation, which was purchased by Black and Decker in 1989. Kwikset is part of the BDHHI Division of Black and Decker which also owns lockset manufacturers Weiser and Baldwin.